How CNC Machining Enhances Precision in Gear Manufacturing
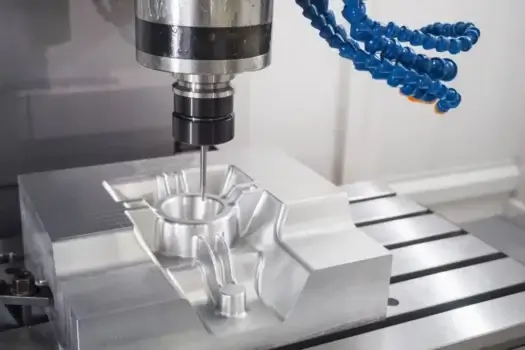
Gear manufacturing is a cornerstone of modern industry, powering everything from automotive transmissions to industrial machinery. At the heart of this process lies the need for absolute precision and repeatability. As the demand for high-performance gears grows, so does the need for advanced manufacturing technologies. Xilici Company (XLC), a leader in precision engineering, leverages CNC machining to redefine the standards of gear manufacturing, ensuring unmatched accuracy and reliability.
The Evolution of Gear Manufacturing
Traditionally, gear manufacturing relied on manual machining and labor-intensive processes. These methods, while effective to an extent, often resulted in inconsistencies and limited scalability. The advent of Computer Numerical Control (CNC) machining has revolutionized the industry by automating complex tasks and delivering consistent, high-quality results.
XLC recognized early on that the future of gear manufacturing would be shaped by digital technologies. By investing in state-of-the-art CNC machines and skilled technicians, the company has positioned itself as a pioneer in the field, capable of meeting the most stringent requirements of modern engineering.
Precision Redefined: The Role of CNC Machining
CNC machining stands out for its ability to produce gears with extremely tight tolerances. At XLC, the process begins with advanced CAD/CAM software, which translates intricate gear designs into precise machine instructions. This digital workflow eliminates human error and ensures that every gear meets exact specifications.
The benefits of CNC machining in gear manufacturing include:
- Consistency: Each gear produced is virtually identical, reducing variability and improving reliability.
- Complex Geometries: CNC machines can create intricate gear profiles that are difficult or impossible with manual methods.
- Material Versatility: From hardened steels to advanced composites, CNC machining handles a wide range of materials.
- Reduced Waste: Precision cutting minimizes material waste, contributing to cost savings and sustainability.
XLC’s commitment to precision is evident in every stage of production, from raw material selection to final inspection. By integrating CNC machining with rigorous quality control protocols, the company ensures that its gears perform flawlessly in demanding applications.
Innovative Approaches: Integrating Custom 3D printing
While CNC machining remains the backbone of gear manufacturing, XLC is also exploring the potential of custom 3D printing. This technology allows for rapid prototyping and the creation of complex, lightweight gear components that would be challenging to machine conventionally.
By combining CNC machining with 3D printing, XLC offers customers the flexibility to iterate designs quickly and cost-effectively. For example, custom 3D printing is used to produce prototype gears for testing, enabling engineers to validate performance before committing to full-scale production. This hybrid approach accelerates innovation and reduces time-to-market for new products.
Industry Trends: Automation and Digitalization
The gear manufacturing industry is undergoing a digital transformation, driven by advances in automation, data analytics, and smart manufacturing. Companies like XLC are at the forefront of this shift, leveraging Industry 4.0 technologies to enhance efficiency and traceability.
- Automated Inspection: Using optical and laser-based systems, XLC can inspect gears in real-time, identifying defects and ensuring compliance with strict standards.
- Predictive Maintenance: Machine learning algorithms analyze equipment data, predicting failures before they occur and minimizing downtime.
- Supply Chain Integration: Digital platforms enable seamless communication between suppliers, manufacturers, and customers, streamlining the entire production process.
These innovations not only improve product quality but also create new opportunities for customization and scalability. As industries demand more specialized gear solutions, XLC’s investment in digital technologies positions it as a trusted partner for complex engineering challenges.
Challenges and Solutions in Precision Gear Manufacturing
Despite the advantages of CNC machining, gear manufacturers face several challenges, including tool wear, thermal distortion, and the need for ultra-fine surface finishes. XLC addresses these issues through continuous process optimization and investment in advanced tooling.
For example, the company employs high-performance cutting tools with specialized coatings to extend tool life and maintain accuracy. Advanced coolant systems are used to control temperatures during machining, reducing the risk of distortion. Surface finishing techniques, such as grinding and honing, ensure that gears meet the highest standards of smoothness and durability.
The Future of Gear Manufacturing: Sustainability and Innovation
Sustainability is becoming increasingly important in the manufacturing sector. XLC is committed to reducing its environmental footprint by optimizing material usage and adopting energy-efficient processes. CNC machining, with its precision and minimal waste, plays a critical role in achieving these goals.
Looking ahead, the integration of CNC machining with emerging technologies like 3D printing and artificial intelligence promises to unlock new possibilities. For instance, 3D printing is not only valuable for prototyping but also for producing lightweight, high-strength components in low volumes. This opens the door to customized gear solutions for applications ranging from robotics to aerospace.
Why Choose XLC for Precision Gear Manufacturing?
Xilici Company (XLC) has built a reputation for excellence by combining technical expertise with a customer-centric approach. Whether you need high-volume production or custom gear solutions, XLC offers a range of services tailored to your needs.
- Comprehensive Capabilities: From CNC machining to custom 3D printing, XLC provides end-to-end solutions for gear manufacturing.
- Quality Assurance: Every gear undergoes rigorous testing and inspection to ensure optimal performance.
- Innovation-Driven: XLC invests in the latest technologies to stay ahead of industry trends and deliver cutting-edge solutions.
- Customer Support: Dedicated engineers and support staff work closely with clients to understand their requirements and deliver results.
By choosing XLC, customers benefit from a partner who understands the complexities of modern gear manufacturing and is committed to delivering precision, reliability, and value.
Conclusion
CNC machining has transformed gear manufacturing by enabling unprecedented levels of precision and consistency. At Xilici Company (XLC), this technology is complemented by innovations such as custom 3D printing and digital manufacturing, ensuring that every gear meets the highest standards of quality. As the industry continues to evolve, XLC remains at the forefront, driving progress through technology, sustainability, and customer-focused solutions.
Whether you’re seeking high-volume production or specialized gear prototypes, XLC’s expertise in CNC machining and 3D printing makes it the ideal partner for your next project. Experience the future of precision gear manufacturing with Xilici Company.