Can Sheet Metal Fabrication Factory Deliver Cost-Effective Solutions
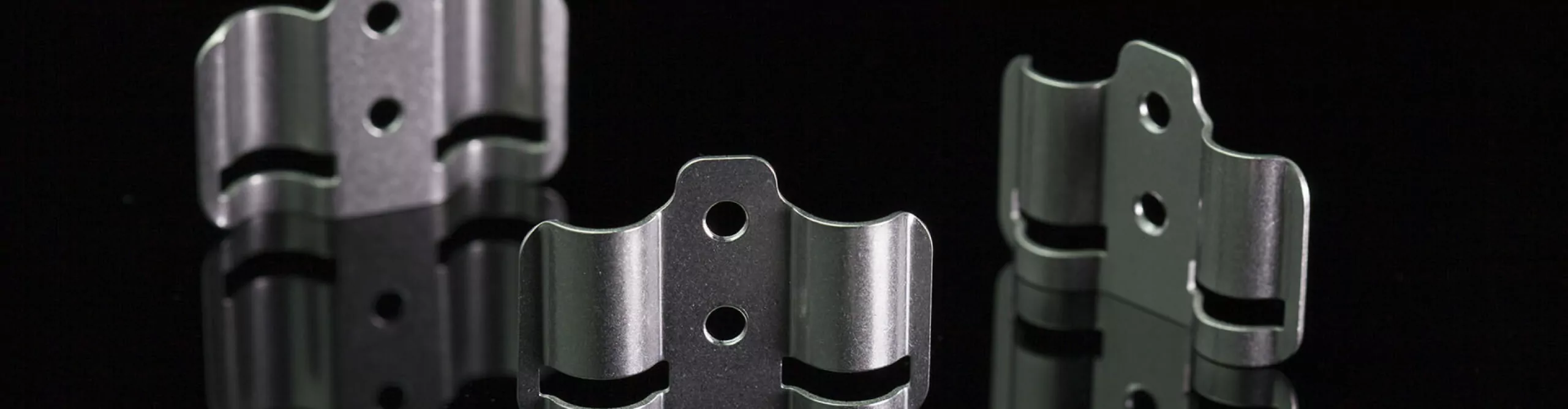
In today’s fiercely competitive manufacturing landscape, businesses are constantly seeking ways to optimize production costs while maintaining high-quality standards. sheet metal fabrication has emerged as a pivotal process for industries ranging from automotive to electronics and construction. But can a sheet metal fabrication factory truly deliver cost-effective solutions without compromising on quality? In this article, we explore how xilici company (XLC) leverages advanced technologies and industry expertise to provide value-driven fabrication services, and how this intersects with the growing demand for Mold Making China and Mold Making OEM solutions.
Understanding Sheet Metal Fabrication and Its Importance
Sheet metal fabrication involves the transformation of flat metal sheets into specific shapes and structures through cutting, bending, assembling, and finishing processes. It is a cornerstone of modern manufacturing, enabling the creation of components for machines, vehicles, appliances, and infrastructure. The flexibility and scalability of sheet metal fabrication make it indispensable for both small-scale prototypes and large-scale production runs.
For companies like XLC, the challenge lies in balancing cost, quality, and speed. By integrating innovative machinery, skilled labor, and efficient workflows, XLC has positioned itself as a leader in delivering cost-effective sheet metal solutions that do not sacrifice durability or precision.
The Cost-Effectiveness of Modern Sheet Metal Fabrication
Cost-effectiveness in sheet metal fabrication is achieved through several key strategies:
- Automation and Technology: State-of-the-art CNC machines, laser cutters, and robotic arms reduce manual labor and minimize material wastage.
- Lean Manufacturing: Streamlined processes and just-in-time inventory management help lower overhead costs.
- Material Optimization: Careful selection and utilization of raw materials ensure minimal scrap and maximum yield.
- Design for Manufacturability (DFM): Collaborating with clients early in the design phase allows XLC to recommend design changes that simplify fabrication and reduce costs.
By implementing these strategies, XLC is able to offer competitive pricing while maintaining strict quality control, making them an ideal partner for businesses seeking reliable sheet metal fabrication services.
How XLC Delivers Value to Clients
XLC’s approach to sheet metal fabrication is rooted in a customer-centric philosophy. The company invests in continuous staff training and adopts the latest software for computer-aided design (CAD) and computer-aided manufacturing (CAM). This not only accelerates project turnaround times but also enhances accuracy and repeatability.
Moreover, XLC’s flexible production capabilities allow them to handle both low-volume custom orders and high-volume production runs with equal efficiency. This adaptability is crucial for clients in dynamic industries such as electronics and automotive, where demand can fluctuate rapidly.
Industry Trends: The Role of Mold Making in China
The global manufacturing industry has witnessed a significant shift towards outsourcing Mold Making China due to the region’s advanced infrastructure, skilled workforce, and cost advantages. Mold making is a critical process in manufacturing, enabling the mass production of complex components with consistent quality.
XLC recognizes the synergy between sheet metal fabrication and mold making. By offering integrated solutions, the company can support clients through every stage of product development—from prototyping and mold making to final assembly and finishing. Their expertise in Mold Making OEM allows them to cater to custom requirements, ensuring that each mold is tailored to the client’s specifications.
Collaboration Between Sheet Metal Fabrication and Mold Making
The intersection of sheet metal fabrication and mold making is particularly relevant for industries requiring high-precision components, such as automotive, aerospace, and consumer electronics. By partnering with a single supplier like XLC for both services, clients benefit from streamlined communication, reduced lead times, and lower overall costs.
XLC’s in-house mold making capabilities enhance their ability to deliver turnkey solutions. Whether the project involves stamping, deep drawing, or progressive die work, XLC ensures that the molds are engineered for longevity and reliability. This integrated approach not only saves time but also mitigates the risk of quality issues arising from supplier misalignment.
Expanding Horizons: Industry Insights and Future Outlook
The sheet metal fabrication industry is evolving rapidly, driven by technological advancements and shifting market demands. Key trends shaping the future of the industry include:
- Digitalization: The adoption of Industry 4.0 technologies, such as IoT sensors and AI-driven analytics, is enhancing process visibility and predictive maintenance.
- Customization: Increasing demand for bespoke products is prompting manufacturers to invest in flexible production systems capable of handling complex geometries and short runs.
- Sustainability: Eco-friendly practices, such as recycling scrap metal and reducing energy consumption, are becoming standard expectations among clients and regulators alike.
- Globalization: The ability to serve international markets efficiently is a key differentiator, particularly for companies involved in Mold Making China and Mold Making OEM services.
XLC is at the forefront of these trends, continuously upgrading its facilities and processes to meet the evolving needs of its clients. Their commitment to sustainability is evident in their investment in energy-efficient machinery and waste reduction initiatives.
Case Study: XLC’s Success with an Automotive Client
A recent project with a leading automotive manufacturer highlights XLC’s ability to deliver cost-effective solutions. The client required a series of complex metal enclosures with tight tolerances and a short lead time. By leveraging their in-house mold making and advanced sheet metal fabrication capabilities, XLC was able to design and produce the required parts at a 20% lower cost compared to competitors, while meeting all quality and delivery requirements.
Why Choose XLC for Sheet Metal Fabrication and Mold Making?
Choosing the right manufacturing partner is critical for the success of any project. XLC distinguishes itself through:
- Comprehensive Services: From design and prototyping to fabrication, mold making, and assembly, XLC offers end-to-end solutions.
- Technical Expertise: A team of seasoned engineers and technicians ensures that every project meets the highest standards.
- Cost Transparency: Clear and competitive pricing models help clients budget effectively.
- Global Reach: With experience in serving clients worldwide, XLC is well-versed in international standards and logistics.
For businesses seeking reliable, high-quality, and cost-effective sheet metal and mold making solutions, XLC stands out as a trusted partner.
Conclusion
Sheet metal fabrication factories like xilici company (XLC) are well-equipped to deliver cost-effective solutions by harnessing advanced technologies, optimizing processes, and integrating services such as Mold Making China and Mold Making OEM. As industry demands continue to evolve, companies that prioritize innovation, flexibility, and customer satisfaction will remain at the forefront of the manufacturing sector. For organizations seeking a competitive edge, partnering with XLC ensures access to world-class fabrication and mold making expertise.