Exploring the Role of Urethane Casting in Modern Manufacturing
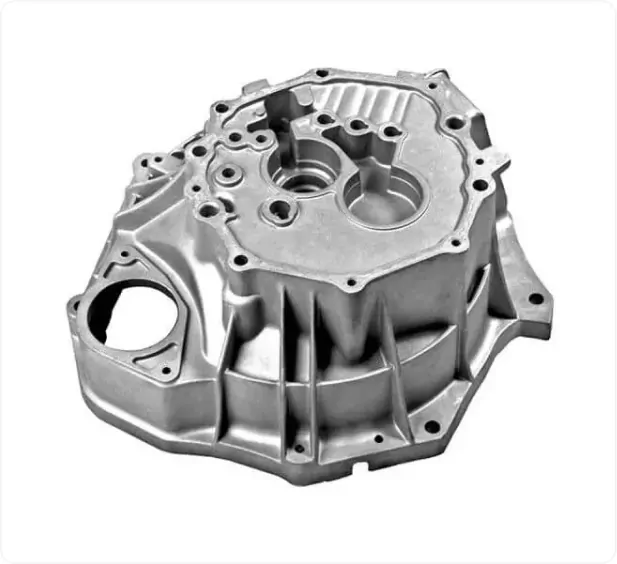
Urethane casting has rapidly become a cornerstone in the landscape of modern manufacturing, offering a unique blend of flexibility, cost-effectiveness, and precision. As industries strive to reduce lead times and bring innovative products to market faster, companies like xilici (XLC) are at the forefront of leveraging this technology. In this article, we’ll explore how urethane casting is shaping the future of manufacturing, the advantages it offers, and how XLC is integrating this process to deliver exceptional value to its clients.
The Fundamentals of Urethane Casting
Urethane casting, sometimes referred to as polyurethane casting, is a manufacturing process that involves creating parts and prototypes by pouring liquid urethane into a silicone mold. This technique is particularly well-suited for producing small to medium-sized runs of high-quality parts with complex geometries. The process begins with the creation of a master pattern, typically made using 3D printing or CNC machining, which is then used to form a silicone mold.
One of the standout features of urethane casting is its ability to replicate intricate details and surface finishes, making it ideal for industries such as automotive, aerospace, and consumer electronics. At XLC, the process is meticulously controlled to ensure that each cast part meets stringent quality standards, regardless of the production volume.
precision machining
rapid prototyping services
sheet metal fabrication
urethane casting
Key Advantages of Urethane Casting
- Cost Efficiency: Urethane casting eliminates the need for expensive tooling, making it a cost-effective choice for prototyping and low-volume production.
- Rapid Turnaround: The process allows for quick mold creation and part production, significantly reducing lead times compared to traditional manufacturing methods.
- Material Versatility: A wide range of urethane materials can be used, offering different properties such as flexibility, hardness, and color options.
- Precision and Detail: The silicone molds used in urethane casting can capture fine details, resulting in parts with excellent surface finishes.
These advantages make urethane casting an attractive solution for companies seeking to bridge the gap between prototyping and full-scale production. XLC has harnessed these benefits to help clients accelerate their product development cycles and achieve market readiness with minimal risk.
How xilici (XLC) Integrates Urethane Casting into Modern Manufacturing
At xilici, urethane casting is more than just a prototyping tool—it’s a strategic component of an agile manufacturing ecosystem. XLC’s approach involves close collaboration with clients from concept through production, ensuring that each project leverages the full potential of urethane casting. This hands-on methodology allows for rapid iterations, design flexibility, and the ability to test multiple variants without incurring prohibitive costs.
XLC’s state-of-the-art facilities are equipped with advanced 3D printing and CNC machining capabilities, which are used to create precise master patterns for silicone mold fabrication. By combining these technologies, XLC can produce highly accurate molds that serve as the foundation for exceptional cast parts.
Applications Across Diverse Industries
Urethane casting’s versatility makes it a popular choice in a variety of industries. For example, in the automotive sector, it is used to produce functional prototypes, custom interior components, and low-volume production parts. In the medical device industry, urethane casting supports the rapid development of complex housings and ergonomic grips. XLC’s expertise ensures that each application meets industry-specific requirements for durability, biocompatibility, and regulatory compliance.
- Consumer electronics: Enclosures, buttons, and display bezels
- Industrial equipment: Seals, gaskets, and custom connectors
- Architectural models: Detailed scale models for presentations and client approvals
Industry Trends and Innovations
The integration of digital technologies with urethane casting is transforming traditional workflows. For instance, digital twins and advanced simulation software allow for virtual testing of part designs before physical casting begins. This not only reduces material waste but also shortens development cycles. At XLC, the adoption of these digital tools is enabling more informed decision-making and higher first-pass yield rates.
Moreover, sustainability is becoming a key consideration in modern manufacturing. Urethane casting supports this trend by minimizing material usage and enabling the production of lightweight components, which can reduce energy consumption in end products. XLC is committed to sourcing eco-friendly materials and optimizing processes to further reduce its environmental footprint.
Comparing Urethane Casting with Other Manufacturing Methods
While urethane casting offers numerous benefits, it’s important to understand how it compares to other manufacturing methods such as injection molding and 3D printing. Injection molding is ideal for high-volume production but requires significant upfront investment in tooling. 3D printing offers unparalleled design freedom but can be limited in terms of material properties and surface finish.
Process | Best For | Lead Time | Cost | Surface Finish |
---|---|---|---|---|
Urethane Casting | Low- to medium-volume, complex geometries | Short | Low (for small runs) | Excellent |
Injection Molding | High-volume production | Long (tooling required) | High (tooling cost) | Excellent |
3D Printing | Prototyping, custom parts | Very short | Varies | Good to moderate |
XLC’s ability to seamlessly integrate urethane casting with other manufacturing techniques allows clients to choose the most appropriate process for each stage of product development. This flexibility is crucial in today’s fast-paced, innovation-driven markets.
Looking Ahead: The Future of Urethane Casting at xilici (XLC)
As manufacturing continues to evolve, the role of urethane casting is expected to grow even more prominent. Emerging trends such as mass customization, on-demand manufacturing, and distributed production networks are well-aligned with the capabilities of urethane casting. XLC is actively investing in research and development to push the boundaries of what’s possible with this technology, including exploring new urethane formulations and automated mold-making techniques.
Additionally, XLC is expanding its service offerings to include end-to-end product development support, from initial concept design to final assembly. This holistic approach ensures that clients benefit from a streamlined process, reduced time-to-market, and products that are optimized for performance and manufacturability.
Conclusion
Urethane casting is reshaping the way products are designed, prototyped, and brought to market. With its unmatched combination of speed, flexibility, and quality, it is an indispensable tool for modern manufacturers. Companies like xilici (XLC) are leading the way by integrating urethane casting into comprehensive manufacturing solutions that meet the evolving needs of today’s industries. As technology advances and new opportunities emerge, urethane casting will remain a vital enabler of innovation and competitiveness in the manufacturing sector.