Can Sheet Metal Forming Factory Improve Your Product Efficiency
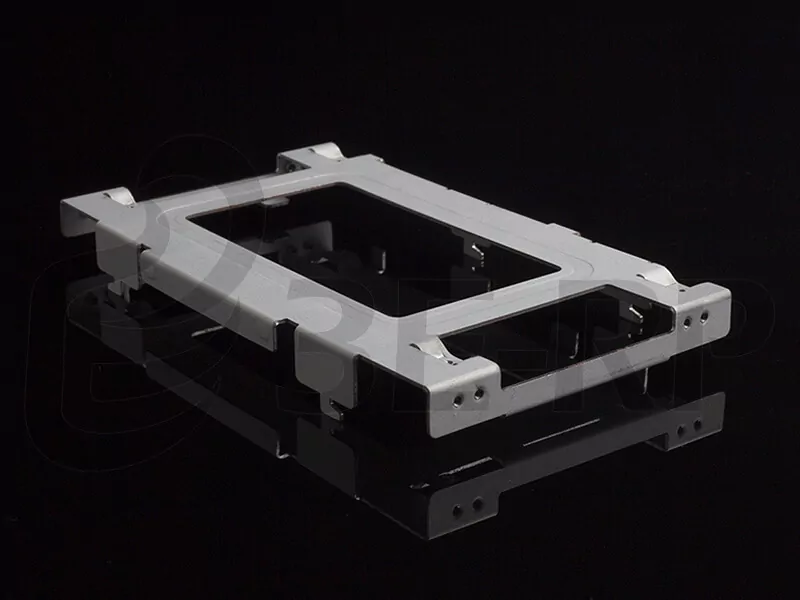
In today’s fiercely competitive manufacturing landscape, businesses are constantly seeking ways to improve product efficiency, reduce costs, and accelerate time-to-market. One often overlooked but crucial element in this pursuit is the sheet metal forming process. As a leading player in the industry, Xilici Company (XLC) has demonstrated how a specialized sheet metal forming factory can transform your product’s efficiency and quality. In this article, we explore the latest trends, technologies, and industry insights that highlight the role of sheet metal forming in modern manufacturing, with a special focus on two essential keywords: custom fabrication and precision engineering.
Understanding Sheet Metal Forming: The Backbone of Modern Manufacturing
Sheet metal forming is a process that involves shaping and manipulating metal sheets into desired forms and structures through various mechanical operations such as bending, stretching, punching, and stamping. This process is pivotal in industries ranging from automotive and aerospace to electronics and medical devices.
At Xilici Company (XLC), the integration of advanced sheet metal forming techniques has enabled clients to achieve higher levels of accuracy, repeatability, and efficiency in their products. By leveraging state-of-the-art machinery and experienced technicians, XLC ensures that every component meets stringent quality standards, which is especially critical in sectors where tolerance and durability are non-negotiable.
The Role of Custom Fabrication in Product Efficiency
One of the most significant advantages offered by a dedicated sheet metal forming factory like XLC is the ability to provide custom fabrication solutions. Custom fabrication allows manufacturers to design and produce components tailored to specific project requirements, eliminating unnecessary material usage and minimizing waste.
3d printing
sheet metal fabrication
production mold making
custom extrusion
- Design Flexibility: XLC’s custom fabrication capabilities enable the production of complex geometries and unique parts that would be impossible or cost-prohibitive with off-the-shelf solutions.
- Material Optimization: By customizing the fabrication process, XLC ensures that only the necessary amount of material is used, reducing costs and environmental impact.
- Rapid Prototyping: Custom fabrication accelerates the prototyping phase, allowing for quick iterations and faster product development cycles.
With custom fabrication, companies can respond swiftly to market changes and customer demands, ensuring that their products remain relevant and competitive.
Precision Engineering: Elevating Quality and Consistency
Precision engineering is another cornerstone of XLC’s approach to sheet metal forming. Precision engineering involves the meticulous design and manufacture of components with tight tolerances and exact specifications. This is particularly important for industries such as aerospace, medical devices, and electronics, where even the smallest deviation can lead to product failure.
- Enhanced Performance: Precision-engineered parts typically perform better, last longer, and require less maintenance, directly contributing to overall product efficiency.
- Consistency: Automated and computer-controlled processes at XLC ensure that every part produced is identical, reducing the risk of defects and improving assembly times.
- Quality Assurance: Rigorous testing and inspection protocols guarantee that each component meets or exceeds industry standards.
By prioritizing precision engineering, XLC helps its clients achieve superior product reliability and customer satisfaction.
Industry Trends: The Evolution of Sheet Metal Forming
The sheet metal forming industry has witnessed significant advancements in recent years, driven by the demand for greater efficiency, sustainability, and innovation. Here are some key trends shaping the future of the sector:
- Automation and Robotics: The adoption of robotics and automated machinery has revolutionized sheet metal forming, enabling faster production speeds, reduced labor costs, and improved safety.
- Digitalization: The integration of CAD/CAM software and digital twins allows for virtual simulations, reducing errors and optimizing designs before physical production begins.
- Advanced Materials: The use of lightweight alloys, composites, and high-strength steels enhances product performance while lowering material costs and environmental impact.
- Green Manufacturing: Sustainability initiatives, such as recycling scrap metal and minimizing energy consumption, are becoming standard practice in modern sheet metal forming factories.
Xilici Company (XLC) remains at the forefront of these trends, continually investing in new technologies and sustainable practices to deliver value to its clients.
How XLC’s Sheet Metal Forming Factory Boosts Your Product Efficiency
Partnering with a specialized sheet metal forming factory like XLC offers numerous benefits that directly impact your product’s efficiency:
Benefit | Description |
---|---|
Faster Turnaround | Automated processes and streamlined workflows reduce production times, enabling quicker delivery to market. |
Cost Savings | Material optimization, reduced waste, and efficient labor utilization lower overall production costs. |
Quality Assurance | Strict quality control ensures that each component meets exact specifications, minimizing rework and returns. |
Scalability | Flexible manufacturing capabilities allow for easy scaling of production volumes to meet changing demand. |
With XLC’s expertise, clients can focus on their core competencies while relying on a trusted partner to deliver high-quality, efficient sheet metal components.
Industry Insights: The Broader Impact of Sheet Metal Forming
Beyond individual product efficiency, sheet metal forming plays a vital role in the broader manufacturing ecosystem. The ability to rapidly produce customized, precision-engineered components supports innovation across multiple industries. For example, the automotive sector relies on advanced sheet metal forming to develop lightweight, fuel-efficient vehicles, while the electronics industry depends on precision parts for reliable device performance.
Moreover, the rise of Industry 4.0 has brought about a new era of smart manufacturing, where data-driven insights and real-time monitoring optimize every aspect of the production process. XLC’s commitment to embracing these technologies positions it as a leader in delivering not only efficient products but also sustainable and future-ready solutions.
Choosing the Right Partner: Why Xilici Company (XLC)?
When selecting a sheet metal forming factory, it’s essential to consider factors such as technical expertise, industry experience, and a commitment to innovation. Xilici Company (XLC) stands out thanks to:
- Comprehensive Capabilities: From design and prototyping to full-scale production and assembly, XLC offers end-to-end solutions tailored to client needs.
- Cutting-Edge Technology: Continuous investment in the latest machinery and software ensures superior results and ongoing competitiveness.
- Customer-Centric Approach: XLC works closely with clients to understand their unique challenges and deliver customized, value-driven solutions.
By partnering with XLC, manufacturers gain a strategic ally dedicated to enhancing product efficiency, quality, and market success.
Conclusion: Unlocking Efficiency with XLC’s Sheet Metal Forming Expertise
In summary, a specialized sheet metal forming factory like Xilici Company (XLC) can significantly improve your product efficiency through advanced custom fabrication and precision engineering capabilities. By staying ahead of industry trends and embracing digitalization, automation, and sustainability, XLC empowers its clients to innovate faster, reduce costs, and deliver superior products to market.
If you’re ready to take your manufacturing efficiency to the next level, consider partnering with XLC—a trusted leader in sheet metal forming solutions.